Are you seeking a premium luxury packaging option that combines versatility, durability, and customizability in a lightweight container ideal for foods, cosmetics, and more? Metal tin box are the perfect solution and have been a popular choice for decades. If you’re considering this premium option for your next big packaging project, you’ve come to the right place!
In this guide, we will explore the details of metal tins and provide you with everything you need to know before starting your next packaging venture.
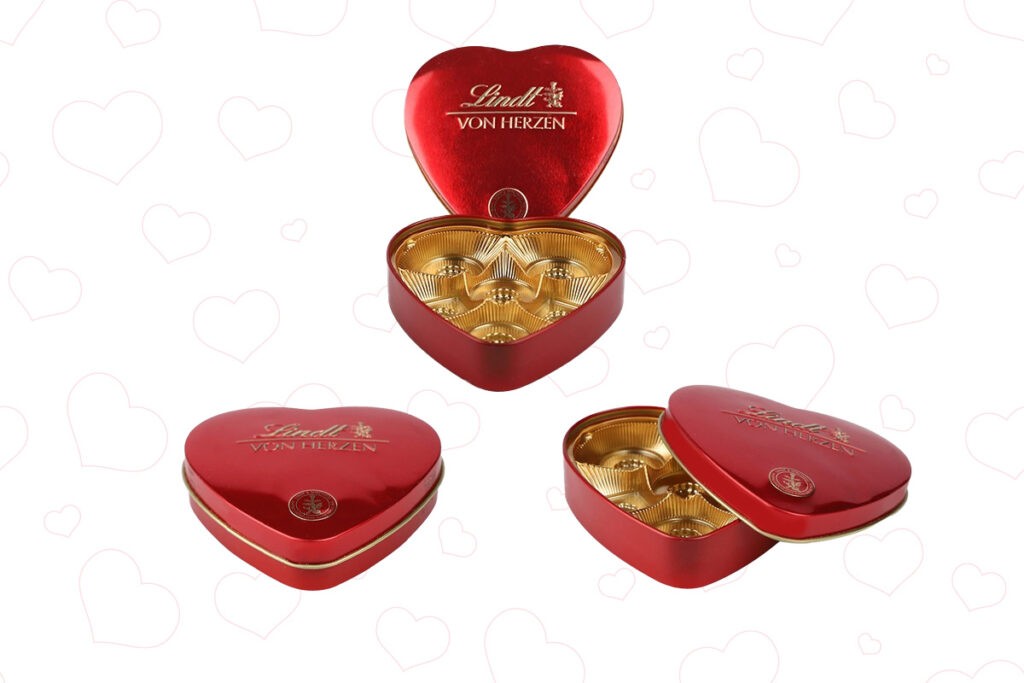
What Are Tin Boxes?
Tin container packaging is a type of metal packaging known for its high durability and variety of unique customizations. These include metallic reflections, varnishes, coatings, embossing and debossing, premium printing techniques, and textures.
However, it’s important to note that while aluminum tin packaging is sometimes used interchangeably with tin containers and boxes, they are quite different. This guide will focus specifically on tin packaging.
The Advantages and Disadvantages of Tin Packaging
While tin containers can enhance the presentation of your product, they might not always be the best choice. Before we delve deeper, let’s examine the benefits and drawbacks of custom metal tin packaging. This guide covers the main points, but for a more comprehensive discussion on the pros and cons of tin containers, click here.
The Pros of Tin Containers
Using tin box for packaging offers numerous benefits, including:
- Durability and Strength: Tin packaging is ideal for protecting products from damage during storage, transportation, and handling.
- Extended Shelf Life: Tin containers provide an effective barrier against light, moisture, and oxygen, preserving the freshness and flavor of products for a longer time.
- Premium Aesthetic Appeal: With their high metallic luster and extensive customizability, tin box help your brand stand out from the competition.
- Reusability and Recyclability: Tin box made from tinplate or steel are recyclable and can be melted down to create new metal products. Their high-quality features, such as magnetic closures or lids, encourage consumers to repurpose the containers, further extending their lifespan.
- Versatility: Tin containers can be customized in terms of shape and size to meet different product requirements and applications.
The Cons of Tin Containers
Like any packaging material, tin containers come with their own set of drawbacks. The main disadvantages include:
- Cost: Tin packaging is more expensive than plastic or cardboard. Additionally, creating a custom mold for uniquely shaped containers can significantly increase costs.
- Weight: While tin is relatively lightweight, it is still heavier than many other packaging materials, potentially leading to higher shipping expenses.
- Rust & Corrosion: Without proper coating or lining, tin containers can rust or corrode when exposed to moisture or acidic products.
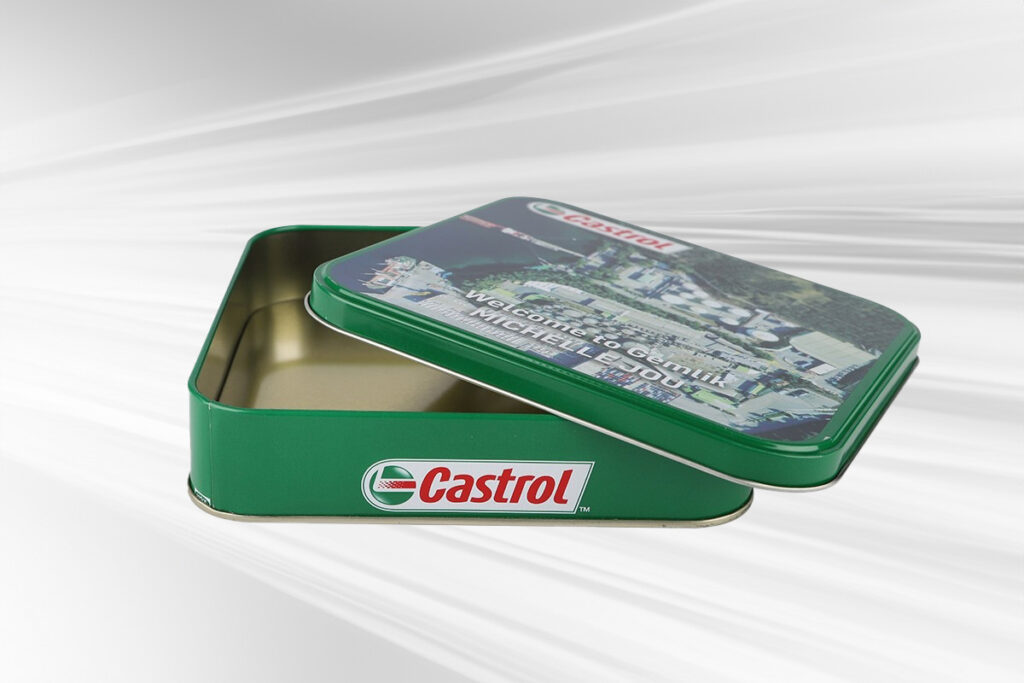
Common Misconceptions About Tin Packaging
Despite the widespread use of tin packaging over the years, certain misconceptions still deter some people from choosing it.
“Tin containers are costly.”
One of the most prevalent misconceptions is that tin containers are prohibitively expensive. While it’s true that tin packaging can be pricier than some other materials, it’s a worthwhile investment due to its durability and longevity.
“Tin packaging is not eco-friendly.”
Many believe that tin packaging isn’t eco-friendly. While the advanced manufacturing processes required for tin can contribute to this perception, tin still has a smaller carbon footprint compared to plastic. Additionally, tin is fully recyclable and supports a circular economy, making it more environmentally friendly than many assume.
“Tin boxes are prone to rust.”
The final misconception we’ll address is that tin is prone to rust. While rust and corrosion are possible if the container is improperly coated, this is not an inherent issue with tin itself. Tin is a pure metal and does not rust; the rusting occurs in the core metal beneath the tin. Proper coating by a professional ensures the container remains rust-free.
So Is Tin Packaging Right for Your Product?
Considering the benefits, disadvantages, and misconceptions, you might still be uncertain about using tin for your next packaging project. The simplest way to decide is to consider your packaging needs:
- Do you want brand recognition and differentiation from competitors?
- Do you want to increase your product’s perceived value in the customer’s eyes?
- Are you looking for a packaging option that offers excellent protection and can be customized to fit your product’s specifications in terms of shape and size?
If you answered yes to these questions, then tin containers are definitely an option worth considering. So let’s continue!
Rectangular & Square Tin Box
Rectangular tins are the most classic option available. Their simple and straightforward design makes them the standard for tin containers. The rectangular shape is ideal for stacking, allowing for easy storage and transport.
Oval & Round Tin Containers
Round or oval containers are another staple in tin packaging. While they may be less storage-efficient than square tins, they offer extra aesthetic charm and a sense of sophisticated luxury that compensates for this shortcoming.
Custom Shaped Tin Canister
If traditional shapes don’t suit your needs, tin containers can also be customized to any shape you imagine! Examples include suitcases, books, cylinders, or hearts.
Tin Styles, Options, and Accessories
Beyond choosing the shape of your tin, there are various stylistic options available to enhance both the protection and aesthetic appeal of your packaging. Let’s explore the different options available when designing your tin.
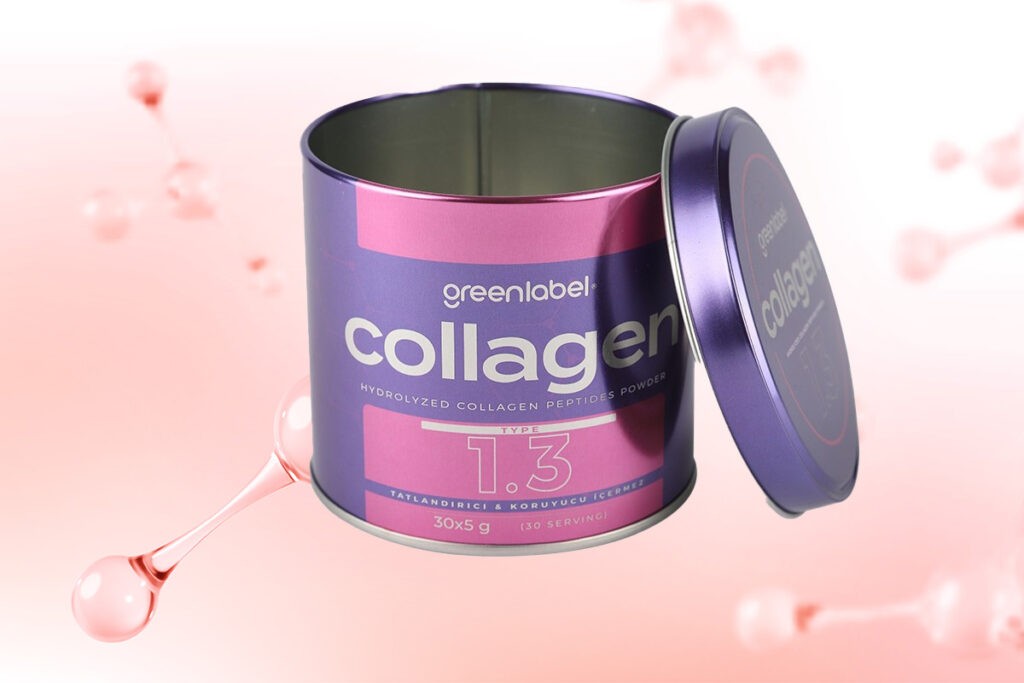
Tin Lid Styles
The first customization option for your tin container is the lid. Popular lid styles include:
- Slipcovers: These lids have hemmed or curled edges that fit snugly over the container without twisting shut. They can feature transparent acrylic to allow consumers to see inside. Slipcovers are seamless, leak-free, and suitable for ointments, cosmetics, and more.
- Slide Top / Sliding Lids: This type of lid can be easily opened or closed by sliding it on or off. Slide tops are ideal for storing candies and mints.
- Hinged Lid / Hinge Top Tins: This lid style is attached to the container with a movable joint on one end and can be opened by lifting the lid. Hinged lids can shut tightly to prevent contaminants and spills, making them ideal for plant-based products like tea leaves, tobacco, or cannabis.
- Screw Top Tins / Screw Caps: Similar to slipcovers, screw caps require twisting to open or close. They can also feature acrylic windows for visibility and provide additional security by ensuring the lid is securely fastened. Screw caps are ideal for ointments and cosmetics.
Interior Accessories for Your Tin
In addition to selecting the lid style for your tin container, you can enhance the interior with various accessories. Consider the following options:
- Foam Inserts: Provide a premium look and feel inside your container while offering extra protection.
- Plastic Tray Inserts: Keep your products securely in place with lightweight, customizable inserts available in various colors.
- Cushion Pads: Use food-safe and sustainable paper cushion pads to keep food products fresh and protected.
- Compartments: Organize your container into different sections with metal separators.
Preservation & Safety
For added food safety in your tin container, consider the following options:
- PVC Tin Sealing Tape: This adhesive tape is specifically designed for sealing tin can lids, protecting the contents from contamination.
- Tamper-Resistant Locks: These locking mechanisms installed on the lid and body of the container provide extra resistance against accidental opening or tampering.
Promotional / Merchandising
In addition to various customizations, promotional and merchandising options are available:
- Window Lids / See-Through Lids: As mentioned in the lid styles section, see-through lids allow customers to view the product inside, enhancing its appeal.
- Handles: Adding a handle to your tin makes it easy for customers to carry your product anywhere.
- Custom Printed Tin Packaging Labels: Enhance your tin’s brand personality with custom-made labels.
Types of Tin Materials
Earlier in this guide, we clarified that tin box are distinct from aluminum containers. However, tin containers aren’t just made of tin! Here are some common materials used for these containers:
- Tinplate/Tin-Plated Steel: This material consists of a steel or iron core coated with a thin layer of tin. This coating prevents rust and corrosion while enhancing the container’s durability. Tinplate offers a smooth, shiny surface suitable for printing and decoration, making it ideal for food packaging, cosmetics, and gifts.
- Frosted Iron: With a matte, slightly rough texture, frosted iron stands out from typical tinplate. Its unique visual appeal and non-reflective, highly durable surface provide a premium look and feel, perfect for sophisticated presentations of premium items.
- Pure Tin: Although rare due to its higher cost and lower strength compared to other materials, pure tin offers excellent corrosion resistance and is non-toxic. It is ideal for high-end, specialized, or limited-edition items.
Printing on Tin: Surface Finishes
Personalizing a tin container with custom designs or your brand logo creates a unique packaging experience. There are various options for the surface finish:
- Lithography (Offset Printing): Common in food packaging, promotional tins, and gift boxes, this technique transfers an image from a metal plate to a rubber blanket and then onto the tin surface. Lithography provides high-quality, detailed images and is cost-effective for high-volume runs.
- Screen Printing (Silk-Screen Printing): Ideal for limited edition designs and custom logos, this technique applies ink directly onto the tin through a mesh screen, allowing for bold colors and large areas of solid color.
- Digital Printing: Best for short runs or personalized designs, digital printing uses digital files to print images directly onto the tin. This technique offers a fast turnaround and is cost-effective for smaller batches.
- Embossing and Debossing: This technique adds a raised (emboss) or recessed (deboss) 3D look to your tin, perfect for premium packaging or enhancing branding elements. It adds a tactile dimension and can be used with other printing techniques.
- Flexographic Printing: Using flexible relief plates to print on a surface, this technique is suited for fast production of continuous patterns and simple designs in large volumes. It’s ideal for mass production, labels, and simple graphics.
- Pad Printing: This method transfers ink from a silicone pad onto the tin surface, making it suitable for irregular shapes, intricate logo designs, and various textures.
- UV Printing: Cured by UV light as it is printed, this ink allows for quick drying, high durability, and vibrant colors, suitable for detailed images and designs.
- Hot Stamping: Using heat and foil to apply metallic designs onto a tin, this technique provides a luxurious finish for premium products, eye-catching brand elements, and decorative finishes.
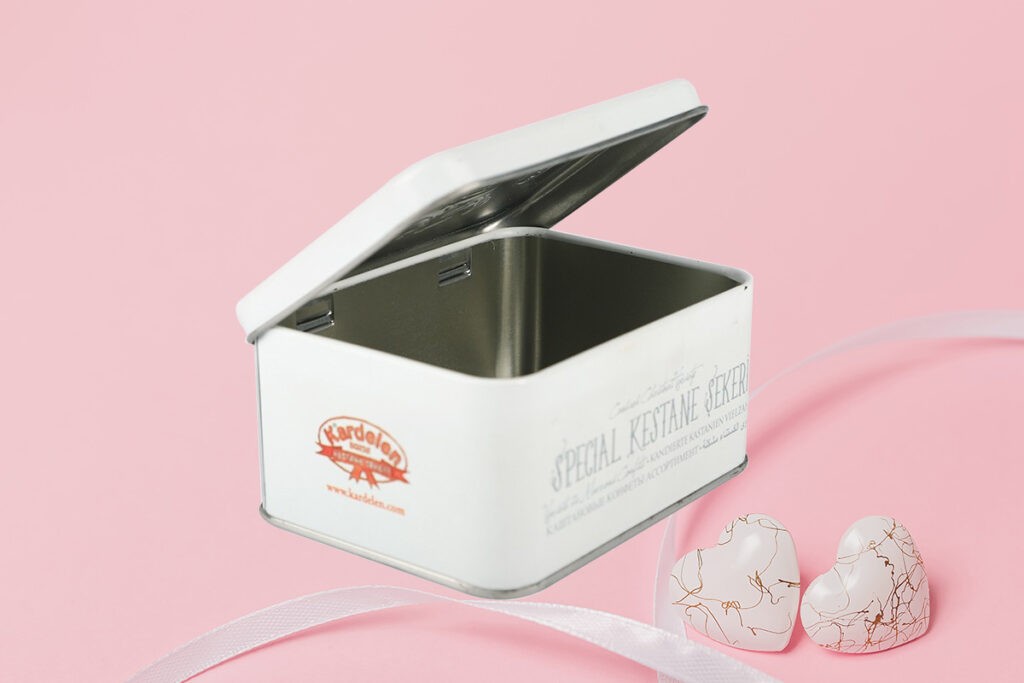
How Are Tin Box Made?
After reviewing the fantastic options for your tin box, it’s time to delve into the production process! Brands often rely on tin packaging manufacturers for this step, as they offer the highest-quality solutions. However, understanding the production process is valuable to know what to expect.
Step 1: Choosing Your Sheet
The first step is selecting your tinplate sheet. Tinplate comes in varying thicknesses, affecting durability and printing quality. Once selected, the manufacturer cuts the sheets using cutting machines to prepare them for the next steps.
Step 2: Printing and Coating
Next, your custom designs and protective varnishes are applied to the cut sheets of tinplate material during the printing and coating step.
Step 3: Forming and Final Assembly
After the designs are applied, the sheets are formed into different parts of the tin box using stamping and forming machines. These machines shape the material into the lid, body, and base.
The container is then assembled by mechanical interlocking or welding, creating the final structure. Seaming seals the edges, ensuring a tight fit, structural integrity, and leak prevention.
Step 4: Quality Control
Upon completing your tin, a thorough quality control inspection is conducted to ensure adherence to standards and identify any defects.
What Works With Tin Containers?
While tin containers can be used for a wide variety of products, there are several that particularly excel with tin packaging:
- Food & Beverage: Tin is widely used and safe for food packaging, making it a popular choice in this industry. From cookies to coffee, tin containers are versatile and durable.
- Cosmetics & Personal Care: Tin packaging is ideal for cosmetics and personal care products like lip balms, perfumes, and soaps. The portable and compact nature of tin containers makes them perfect for travel and on-the-go use.
- Gifts and Promotional Items: With their luxurious appearance, unique shapes, and customizable printing options, tin containers are excellent for packaging gifts and promotional items.
Ready to Start Your Tin Box Project?
While the mentioned products are ideal for tin packaging, the versatility of custom packaging allows for experimentation and creativity. Explore our tin packaging catalog for inspiration!
If you’re ready to begin your journey with custom tin can packaging, Artaş Pack can help. Let’s create something exceptional together!
Phone : +90 (533) 580 23 38
E-mail : sales@artaspack.com